References – worldwide.
Leading engineering, sound advice, excellent products "Made in Germany" and extensive services are values that make Kärcher a reliable partner for tank and container cleaning. Established companies and market leaders rely on the know-how and innovative products and services of Kärcher worldwide.
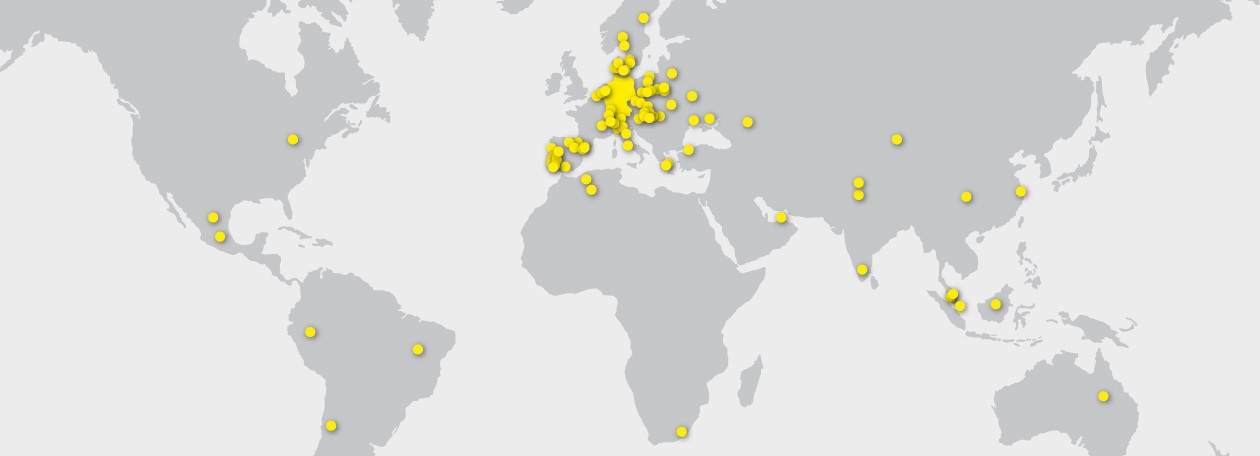
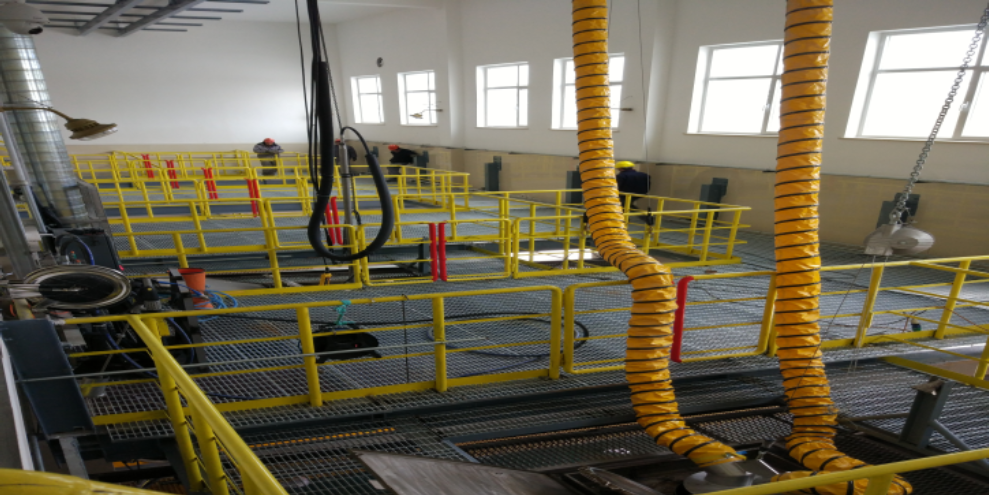
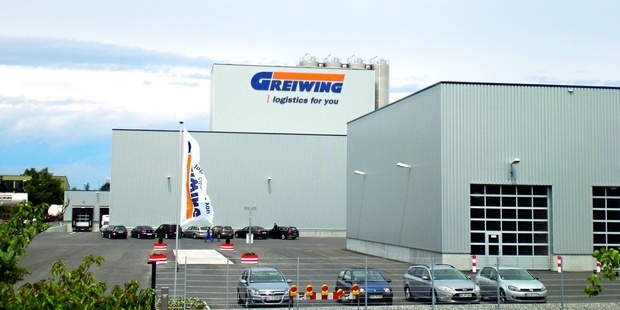
Greiwing Logistics/Germany
As one of Europe's leading providers, Greiwing offers complete tailor-made solutions across all areas of silo logistics.
Ultra-modern cleaning systems for tanks and silos, and specially trained, experienced staff ensure the highest standards of silo cleaning.
As a member of the DVTI (German association for tank interior cleaning), Greiwing issues the European Cleaning Document (ECD). SQAS approval also guarantees a high standard of work safety, quality and environmental protection.
In 2012, the global logistics service provider from the Westphalian town of Greven opened a public cleaning system for silo trailers at its new site in Leipheim.
With two cleaning lines featuring cleaning heads, hot water generation via an HWE 4000 E, chemical dosing and a drying facility, the Kärcher system is designed for interior cleaning of silo trucks. Up to 40 trucks per day can be cleaned here quickly and efficiently.
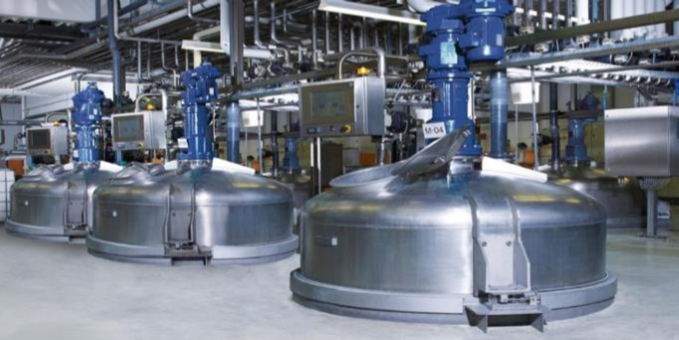
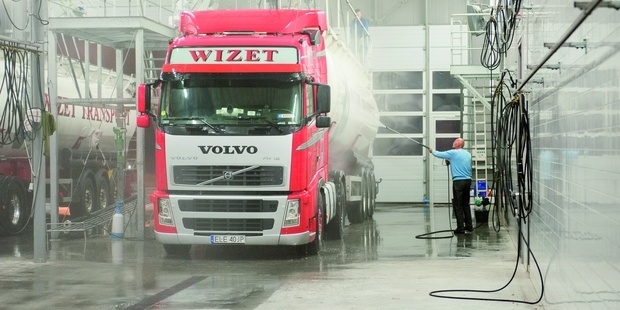
Wizet Transport Sp. z o.o./Poland
Wizet Transport Sp. z o.o. is a company with 60 road tankers and provides services for the global transportation of liquid substances. The company is headquartered in Łęczyca (central Poland). The tank cleaning system was put into operation in April 2012 and is used both for the company's own vehicles and for commercial purposes.
The main components of the TSC cleaning system for road tankers are:
- 5 HKF 200 E interior cleaners
- 5 HDI 38/12 high-pressure pumps
- High-pressure heat exchanger
- High-pressure detergent dosing unit
- Control system
- Setting the cleaning programme via PC
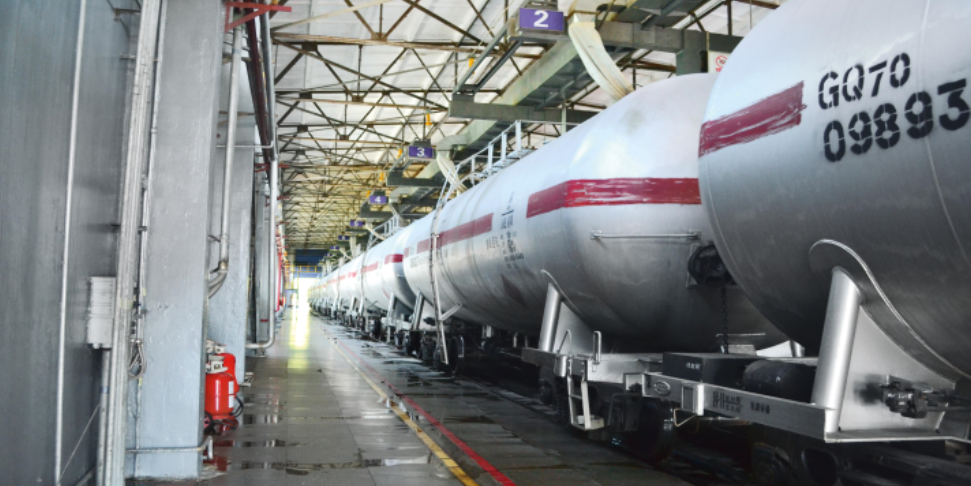
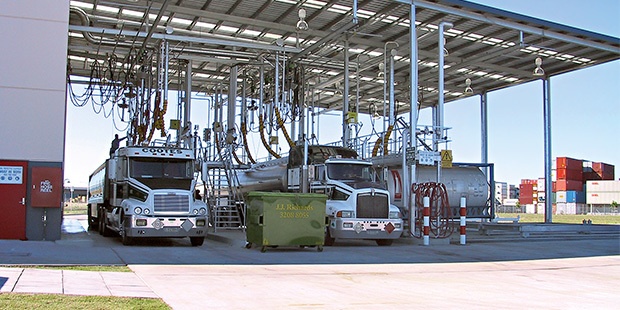
Australian Terminal Services/Australia
The company Australian Terminal Services, a subsidiary of the Australian industry leader Transpacific Industries Group Ltd, commissioned Kärcher to build a large cleaning system in Queensland in 2001.
The system was designed specially for road tankers, 20 ft containers and small containers. It consists of three cleaning lines. Two cleaning lines for road tankers and one for 20 ft containers. Up to four chambers can be cleaned with simultaneous cleaning steps on the road tanker cleaning lines.
The system is controlled by a PLC and in-built operator panel. The operator can configure up to five automatic programme sequences per cleaning line.
Interior cleaning works automatically and has an optional two-slot detergent dosing unit on the high pressure side. Exterior cleaning is carried out manually and has an optional two-slot detergent dosing unit on the suction side.
Cleaning lines and individual cleaning steps can be selected at will via remote control. The hot air drying facility can dry up to five tank chambers per cleaning line.
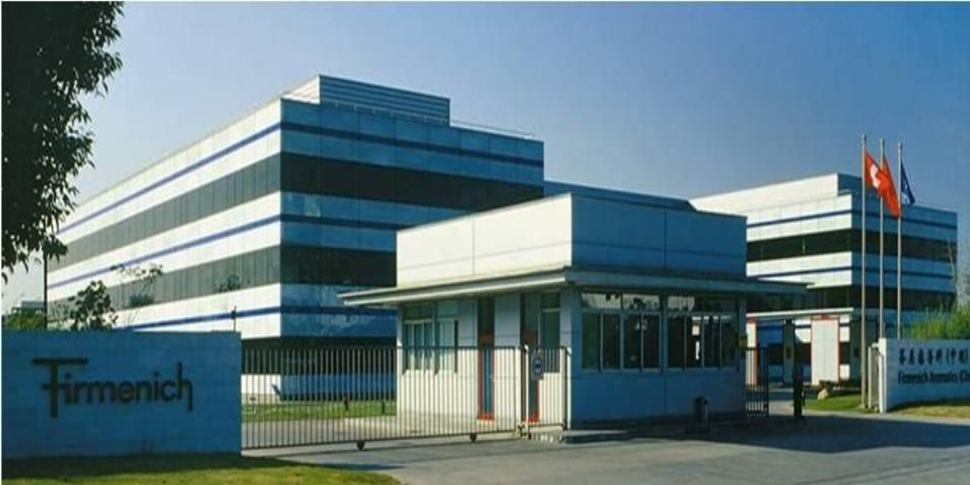
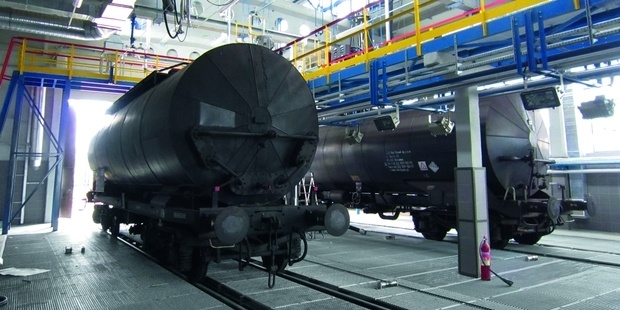
LOTOS Kolej Sp. z o.o./Poland
LOTOS Kolej tank wagons are now washed by a new TSC system from Kärcher.
The LOTOS Group is one of Poland's largest companies. The oil company operates both in Poland and abroad. Its field of activity covers extraction and processing of crude oil, as well as trading high-quality oil products.
As part of the LOTOS Group, LOTOS Kolej is responsible for transporting products and delivering oil to the refinery in Gdańsk. Regular cleaning of the tank wagons is required, for example, for repairs and servicing.
Cleaning at this site used to be carried out using a medium-pressure system. With a view to increasing efficiency, the customer decided to invest in new cleaning technology.
The system, which was completed in May 2012, includes two cleaning lines with six HKF 200 K2 interior cleaners. These are supplied by a total of 10 HDI 38/12 high-pressure pumps. Warm and hot water can be generated using any of the three high-pressure heat exchangers and one low-pressure heat exchanger. The high-pressure detergent dosing unit works precisely and ensures long working times for the high-pressure pumps. The PLC control system was tailored to the customer's individual requirements.